07 Jun Prevention is the correct approach to (any) crisis situation
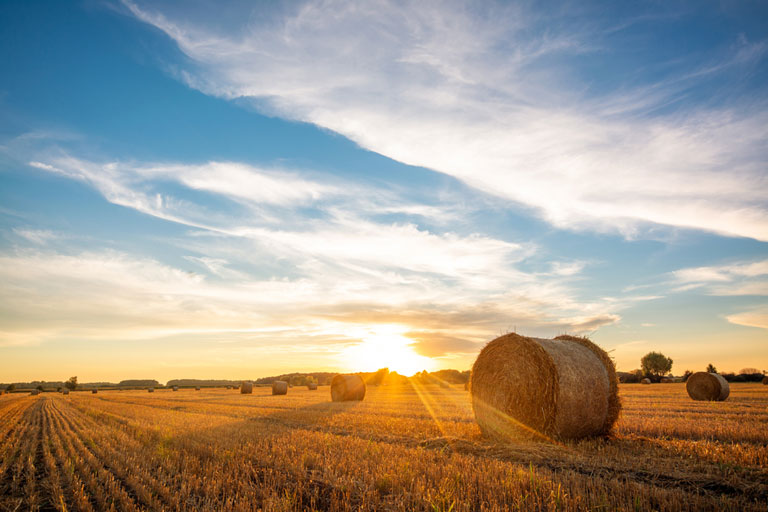
Betty Oikonomou, Nuevo SA, b.oikonomou@nuevo-group.com
At the height of the COVID-19 pandemic, all industries worldwide have been affected from the significant challenges of supply chains.
Around the world, countries were struggling with transportation and logistical issues, facility shutdowns, the inability to find skilled and willing labor (due to pandemic), banned exports, partial closure of international ports, which have led to shortages of essential feed ingredients. Furthermore, many industries resorted to panic-buying and stocking of animal feed/ raw materials/ feed additives in the anticipation of potential shortages. This led to an increase of global feed sales and high raw material and feed additive costs.
Could these ‘panic-actions’ lead a feed industry to a lower quality ingredients selection or frequently change of feed formulations? Could these rapid changes affect the quality of final products or even, in a worst-case scenario, lead to crises? And how ready are we for the unexpected?
Prevention is better than cure
Before going any further, I should point out that unexpected difficulties either from the external or internal business environment might lead to sudden crisis situations even in a properly managed company. Therefore, the design and implementation of a preventive strategy is critical to effectively deal with such situations. This may include:
- Hazard analysis
Known or reasonably foreseeable biological, chemical, physical and allergen hazards (food). A facility should also consider hazards that may be intentionally introduced for economic gain. Feed fraud and feed terror risks differ from feed quality and feed safety risks in that the action is intentional and the motivation is either economic gain or harm.
- Preventive Controls
Controls applied to minimize or prevent health risk associated with identified hazards. These may include process controls, sanitation controls, personnel training etc.
- Supply chain program
Ensure that hazards are controlled throughout the feed supply chain. Manufacturers should verify controls applied by a supplier and establish controls for hazards not addressed by a supplier. This may also include auditing, certificates, external lab analysis etc.
- Recall Plan
Establish procedures to notify appropriate parties of a recall, conduct effectiveness checks to verify the implementation of a recall, including traceability procedure, and dispose of a recalled product.
- Monitoring
Determine whether control measures are operating as intended, by procedures for monitoring and documenting the application of preventive controls.
- Corrective actions
If a facility discovers that preventive controls are not properly implemented, it should enact procedures and document it.
- Verification
Verify and validate the procedures of all components addressed, including validation of preventive controls as well as verification of monitoring procedures and corrective actions.
- Record keeping
All records and documented information shall be kept in accordance with legal and customer requirements or, in many cases, based on a feed quality and safety standards.
Crises arise for a multitude of reasons and unfortunately, even for a full certified company with well-defined processes, feed safety seems to be a multifactorial process. Having said this, the challenge then is to assess how ready we are to effectively deal with crises when they actually emerge.